Taglio Abrasivo
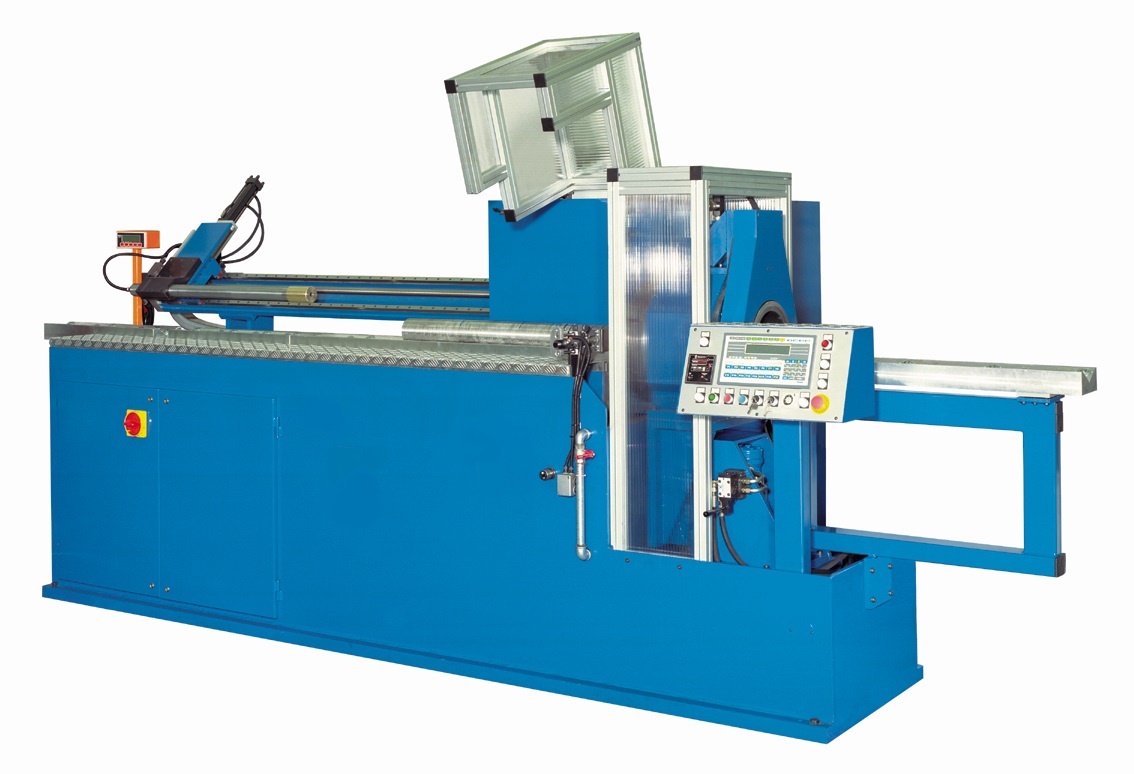
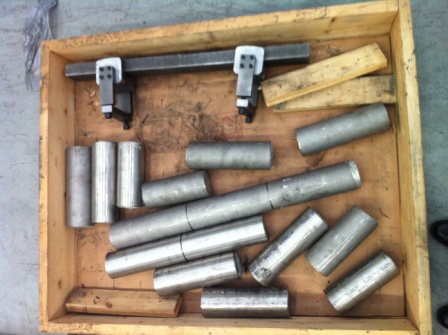
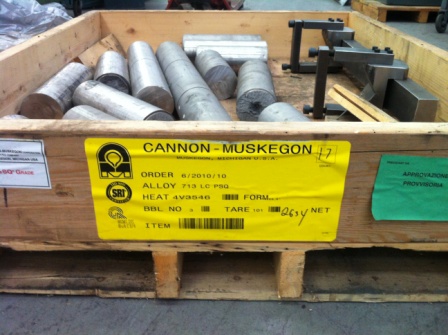
SEZIONATURA DI TONDI IN ACCIAIO HASTELLOY X - INCONEL
DESCRIZIONE TECNICA:
il basamento è costituito da una struttura in acciaio elettrosaldato di grosso spessore, rinvenuta, stabilizzata, sabbiata e verniciata con fondo epossidico e verniciatura finale colore blu RAL 5012 per le parti riguardanti la struttura della macchina e di colore grigio RAL 7035 per le cabinature, carter, centrale idraulica ed armadio apparecchiatura elettrica; il alternativa la verniciatura finale è personalizzabile secondo la richiesta del cliente;
n° 1 stazione di caricamento barre, completa di rulli posti in senso longitudinale e regolabili manualmente in altezza mediante l’utilizzo di una coppia di viti a filettatura quadra e relativi riduttori, azionati da motore trifase a comando manuale;
la stazione di caricamento barre, scorre su guide lineari temprate e rettificate a ricircolo di rulli con lubrificazione forzata ed automatica, ed il suo movimento in senso orizzontale viene dato dalla vite a ricircolo di sfere comandata da n° 1 motore brushless; la barra viene depositata sulle coppie di rulli e con l’apposito spingitore viene spinta fino ad un riscontro fisso mediante l’utilizzo del motore brushless;
per consentire il caricamento delle barre, lo spingitore viene escluso mediante scorrimento su guide lineari temprate rettificate a ricircolo di rulli con lubrificazione forzata ed automatica ed il suo movimento è dato da un cilindro idraulico;
n° 1 rulliera di carico barre completa di rulli posti in senso longitudinale e regolabili manualmente in altezza mediante l’utilizzo di una coppia di viti a filettatura quadra e relativi riduttori, azionati da motore trifase a comando manuale;
n° 2 rulliere di scarico barre, così composte:
n° 1 completa di rulli posti in senso longitudinale e regolabili manualmente in altezza mediante l’utilizzo di una coppia di viti a filettatura quadra e relativi riduttori, azionati da motore trifase a comando manuale;
n° 1 completa di rulli posti in senso trasversale e con bordi di contenimento, posizionati ad un’altezza fissa, la cui parte tangente superiore dei rulli corrisponde con la parte tangente superiore della coppia di rulli situati sul bancale di lavoro della pressa idraulica;
le rulliere di carico e scarico hanno la funzione di sostenere durante la fase di taglio le barre da tagliare e tagliate;
n° 1 stazione di sezionatura, composta da:
n° 1 mandrino autocentrante idraulico composto da n° 3 griffe per il bloccaggio delle barre; un apposito motore provvede a comandare la rotazione dell’autocentrante e quindi della barra che è compresa da un MIN di 5 giri/min ad un MAX di 20 giri/min, a regolazione manuale;
una volta posta in rotazione la barra, il taglio avviene tramite una mola abrasiva azionata dall’apposito motore elettrico da 18,5 kw con velocità di rotazione della mola medesima pari a 3200 giri/min; la mola è montata su cono ISO 50 DIN 2080 con azione di bloccaggio manuale mediante tirante;
NOTA: per consentire la chiusura della intera gamma dei diametri, i morsetti dovranno essere opportunamente posizionati;
n° 1 unità di taglio e scorre su guide lineari temprate rettificate a ricircolo di rulli con lubrificazione forzata ed automatica ed il suo movimento è dato da un cilindro idraulico; è completamente protetta e dotata di una cappa predisposta a ricevere il tubo dell’adeguato impianto di aspirazione polveri ed inoltre completa di un sistema di lavaggio polveri;
l’unità è dotata di n° 1 coppia di fotocellule laser per la commutazione dalla velocità alta dell’unità (avanzamento rapido) alla velocità bassa (avanzamento taglio), montate ad un’adeguata distanza per evitare l’intasamento dalle polveri create durante le operazioni di taglio;
il diametro del nocciolo viene rilevato da una unità di misura elettronica a raggio laser avente precisione ± 1 mm e larghezza inferiore alla dimensione della cava creata durante la molatura; questa unità di misura è interfacciata con il PLC per la gestione automatica della macchina in funzione al diametro del nocciolo rilevato; gestisce quindi il termine della lavorazione con arretramento automatico della testa di molatura; viene montato in apposito contenitore per essere protetto dalle polveri create durante la molatura ed equipaggiato di un soffio pneumatico continuo ad alta pressione per impedire l’ostruzione della fessura di uscita del raggio laser e quindi l’ingresso nel contenitore delle polveri stesse assicurando la massima funzionalità durante la lettura del diametro;
L’evacuazione degli spezzoni avviene dalla rulliera di scarico posta dopo la stazione di sezionatura; le barre vengono quindi trasferite alla pressa;
n° 1 gruppo di lavaggio delle polveri create durante la fase di taglio con pompa ricircolo liquido da 300 litri/min e vasca in acciaio inox; questo gruppo è montato sul retro della macchina con canalizzazione diritta per lo scarico dei liquidi verso la vasca e di facile accesso per eventuali manutenzioni; così pure di facile accesso la vasca di recupero liquido per eventuale pulizia;
il gruppo di lavaggio è inoltre completo del filtro di depurazione acque con rotolo a tessuto filtrante 23 micron per le polveri create durante la fase di taglio; questo gruppo è montato sul retro della macchina di facile accesso per la sostituzione dell’unità filtrante;
n° 1 impianto filtrante statico ad elevata efficienza di filtrazione in lamiera di acciaio, dotato di ventilatore centrifugo ad alto rendimento avente una portata di 4000 m³/ora MAX, box insonorizzante, camera di calma per la separazione gravitazionale delle particelle solide, filtri antistatici, portello frontale di accesso ai filtri interni, serbatoio di accumulo aria compressa necessario al sistema automatico di soffiaggio in contro corrente per la pulizia e rigenerazione del filtro, cassetto estraibile per il recupero delle polveri, indicatore intasamento filtri;
n° 1 sistema di pesatura dotato di basamento su piedini snodati sferici per la regolazione del livello, avente le dimensioni di 600x400 mm, n° 4 celle di carico aventi la portata di 150 kg cad e grado di protezione IP 67, indicatore di peso in struttura di lamiera acciaio inox, grado di protezione IP 65, display LCD e divisione di pesatura di 0,1 kg;
n° 1 banco di lavoro adatto all’appoggio del sistema di pesatura;
n° 1 pressa oleodinamica da 40 tonn. per la rottura delle barre sezionate avente altezza piano di lavoro 1000 mm da terra, tavola di lavoro avente le dimensioni di 700x500 mm, tavola mobile superiore avente le dimensioni di 700x350 mm sulla quale verrà montato l’apposito punzone per la rottura delle barre, velocità di avvicinamento ed allontanamento rapido di 26 mm/sec e velocità di lavoro lenta di 9 mm/sec;
n° 1 gru a bandiera avente portata MAX di 200 kg, sbraccio 5000 mm, altezza sotto trave 3000 mm, comprensiva di paranco elettrico a catena e pulsantiera di comando;
n° 1 apparecchiatura elettrica indipendente dalla macchina ed in comoda posizione per una facile manutenzione, nel rispetto delle normative CE, con gestione tramite PLC comprendente i seguenti articoli:
- parti elettromeccaniche marca Siemens;
- drive per motore e motore asse CN avanzamento barra di marca Siemens;
- plc di marca Siemens;
- pannello operatore touch screen colori da 10,4” di marca Siemens;
- contapezzi elettronico con disinserimento automatico al raggiungimento della quantità preimpostata;
- dispositivo di segnalazione fine barra;
- dispositivo salvalama, per intervento istantaneo di protezione da eventuali sovraccarichi;
- pulsantiera comandi generali su consolle pensile in posizione ergonomica per l’operatore;
- pulsanteria telemecanique, per comandi da operatore;
n° 1 centrale idraulica indipendente dalla macchina, completa di distributori, regolatori, pressostati, indicatore di livello elettrico per la segnalazione del basso livello olio, manometro e filtro, scambiatore di calore e termostato, il tutto in comoda posizione per una facile manutenzione;
n° 1 pompa lubrificazione guide completa di serbatoio con livello per la segnalazione del basso livello olio e pressostato di segnalazione anomalia lubrificazione;
n° 1 laser per individuare facilmente il punto preciso del taglio nel caso di avanzamento manuale;
gestione automatica tramite PLC dell’avanzamento della barra da tagliare in funzione della lunghezza dei tagli da eseguire;
servizio di teleservice remoto escluso contratto teleservice da stipulare con azienda realizzatrice del software;
protezioni in solida struttura di acciaio, dotata di portelloni per aperture frontale per ispezione e superiore per il carico delle barre; tutti i portelloni di apertura sono equipaggiati con micron di sicurezza per lo spegnimento immediato della macchina in caso di apertura accidentale secondo la vigente normativa Legge 626 per la sicurezza del personale negli ambienti di lavoro;
n° 1 manuale istruzioni in lingua italiana/inglese.
Rimane escluso dalla presente fornitura:
e tutto quanto non espressamente indicato nella presente quotazione.
Descrizione sintetica del ciclo operativo:
1) disinserimento dello spingitore per il carico della barra;
2) carico manuale della barra;
3) inserimento dello spingitore della barra;
4) avanzamento della barra verso il mandrino mediante comando manuale del motore brushless;
5) serraggio manuale dei morsetti del mandrino a misura di taglio raggiunta;
6) start ciclo: rotazione mandrino con eventuale velocità di rotazione in funzione del diametro da tagliare, rotazione mola, avanzamento unità di taglio;
7) stop ciclo in automatico mediante rilevamento diametro del nocciolo, ritorno rapido unità di taglio ed arresto rotazione mola;
8) stop ciclo in manuale mediante apposito pulsante sulla consolle comandi, ritorno rapido unità di taglio ed arresto rotazione mola;